RV减速机是由行星齿轮减速机构和摆线针轮减速机构组成的两级精密减速机,具有体积小、传动比范围大、使用寿命长、效率高等特点,广泛应用于工业机器人、机床、航空航天等领域。行星架刚性盘组件是RV减速机的核心支撑部件,结构复杂,精度要求高,其加工精度和质量稳定性一直是RV减速机实现国产化的难题。针对某款RV减速器的行星架刚性盘组件,结合企业现有资源,采用高精度立式加工中心进行镗铣加工,采用数控外圆磨床进行外圆和端面磨削,取得了较好的加工效果。
1 行星架刚性盘组件结构
某款RV减速器行星架刚性盘组件的基本结构如图1 所示。这一行星架刚性盘组件由行星架和刚性盘装配而成,各结构的尺寸、圆度、圆柱度、同轴度要求很高,包含定位销孔、偏心轴孔、主轴承位、螺栓孔等加工部位。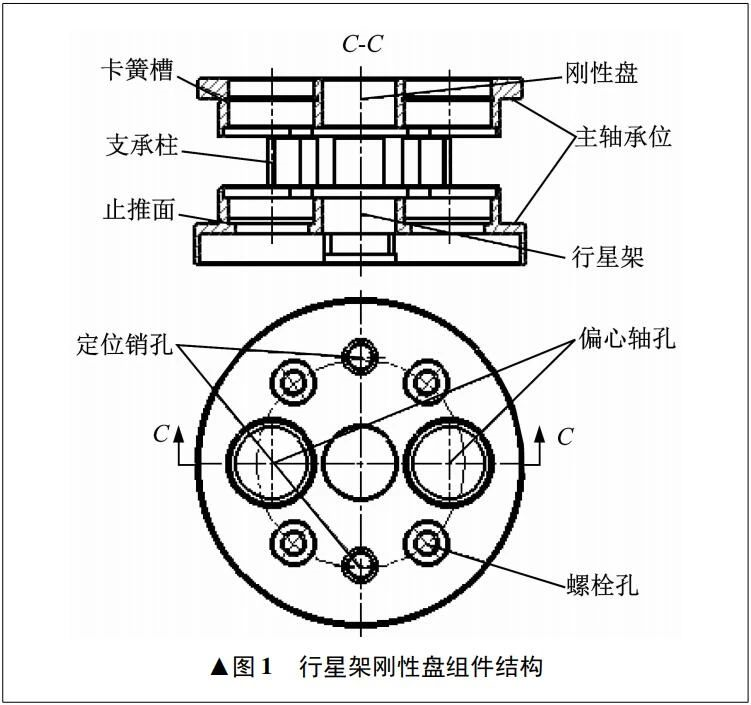
偏心轴孔用于装配和支撑偏心轴系,主轴承位用于装配主轴轴承,承载减速机各核心传动轴承负载。偏心轴孔圆度、圆柱度均要求在0.005 mm 以内,两偏心轴孔孔距公差为± 0.003 mm,主轴承位平面度要求为不大于 0.005 mm。
2 精加工工艺方案
行星架刚性盘组件为中空回转体框架结构,由行星架和刚性盘装配而成, 主要精加工位置为偏心轴孔、主轴承位、定位销孔等。若采用常规的先铣削再磨削工艺方案,则加工质量不稳定,且存在反复组装后精度大幅降低的情况。经过批次试制,改进后的工艺流程如下: 分别磨削行星架、刚性盘端面,组装行星架、刚性盘, 磨削主轴承位, 钻铰定位销孔, 加工卡簧槽、镗铣偏心轴孔。
具体的精加工工艺方案如下: ① 保证两零件端面的平面精度,确保行星架、刚性盘组装时贴合面精度;② 进行螺栓锁紧装配,装配时注意螺栓锁紧力进行分阶段加力,并做好锁紧力的控制; ③ 磨削组件的主轴承位,保证轴承位的平面度和外圆圆度、圆柱度;④ 在高精度坐标镗床上钻铰定位销孔,以保证组件反复拆装后具有较高精度和一致性; ⑤ 加工卡簧槽,镗铣偏心轴孔。这一精加工工艺方案通过高精度磨床加工保证基准位高精度,减小工序衔接过程中的装夹误差。精密磨床、精密坐标镗床等设备自身的高精度确保了行星架刚性盘组件的加工精度和质量稳定性。
3 加工误差分析
行星架刚性盘组件是组合部件,有主轴承位、偏心轴孔等轴承安装位,结构复杂,精度高。在试制过程中会出现各种加工误差,以其中典型的三种加工误差为例进行分析。
3.1 偏心轴孔同轴度误差
行星架刚性盘组件的两偏心轴孔出现波纹状振纹,如图 2所示。偏心轴孔的行星架段和刚性盘段的同轴度超差。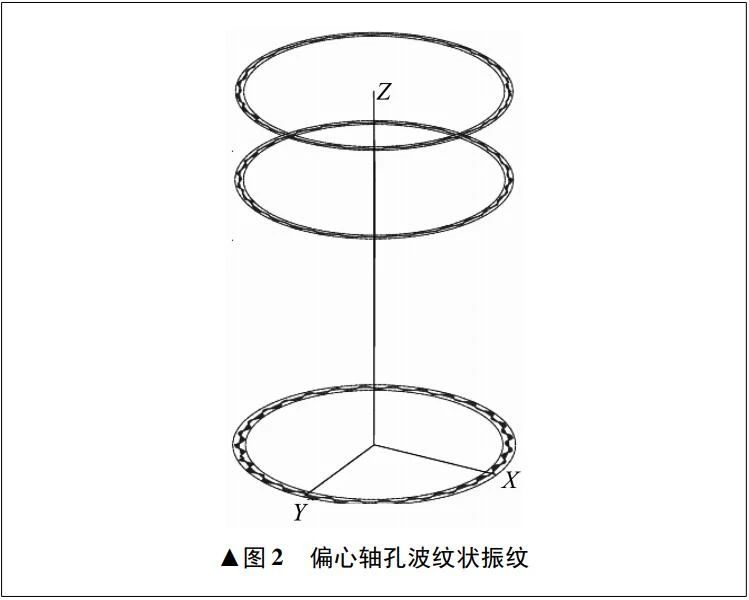
针对误差情况进行分析,出现波纹状振纹是由于加工过程中刀具和工件之间发生了相对振动。偏心轴孔的加工刀具为镗刀,精镗进刀量较小,镗刀直径大于25 mm,刚性好。工件为中空型腔结构,由行星架、刚性盘装配而成,当压板仅压住行星架下端时,镗削加工受力形成悬臂梁结构。主切削力 FZ 为:
式中: C为与工件材料、刀具有关的因数;ap 为进刀量;f为进给量。ap的指数 x 近似等于 1,f的指数y为 0.75~0.9,表明 ap对主切削力 FZ 的影响比 f 大,因此可以适当减小精镗进刀量 ap,增大进给量 f。为了保证工件的固定稳定性,当上下端面均用压板压紧时,需避免压力过大造成工件夹持变形。
以下分析偏心轴孔上端刚性盘部分圆柱孔与下端行星架圆柱孔同轴度超差。根据同轴度的定义,同轴度指被测轴线相对于基准轴线位置的变化量,两轴的偏离通常是三种情况的综合: 被测轴线弯曲、被测轴线倾斜、被测轴线偏移。偏心轴孔同轴度简化模型如图3 所示。对简化模型进行分析,上端刚性盘圆柱孔发生倾斜,下端行星架圆柱孔无异常。当以下端行星架圆柱孔轴线为基准时,同轴度偏差为 Δ1。当以上端圆柱孔轴线为基准时, 两圆柱孔同轴度偏差 Δ2为 Δ1H /L1, 同轴度偏差显著变大,且变大倍数为 H/L1。结合结构特殊性,行星架、刚性盘的圆柱孔段高度均较小,但组装后H值较大,测量时采样点的局限性导致了偶然误差的增大,结构特性则进一步放大了误差。
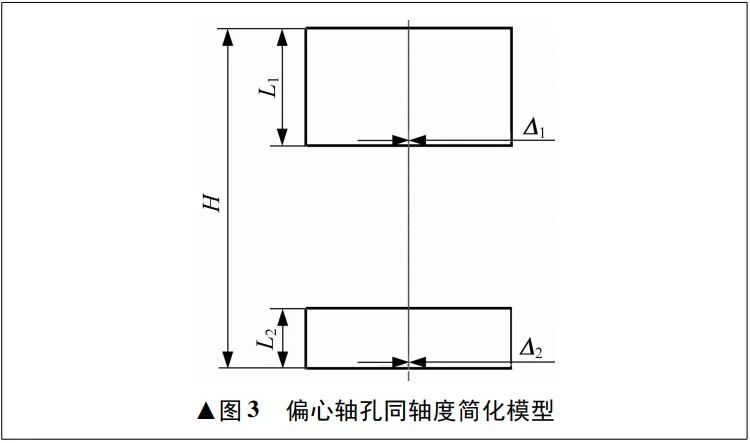
据此进行工艺改进。采用上下夹持的方案,通过压板对行星架、刚性盘压紧, 用扭力扳手控制压紧力,避免造成工件变形。适当减小精镗进刀量,增大进给量,在尽量减小切削力的同时仍能保持较高的加工效率。在做好上述措施的同时,对同轴度的计量方案进行改进,扩大采点范围,增加采点数量。采取上述措施后,偏心轴孔的加工效果如图 4 所示。偏心轴孔同轴度质量明显改善,并达标。
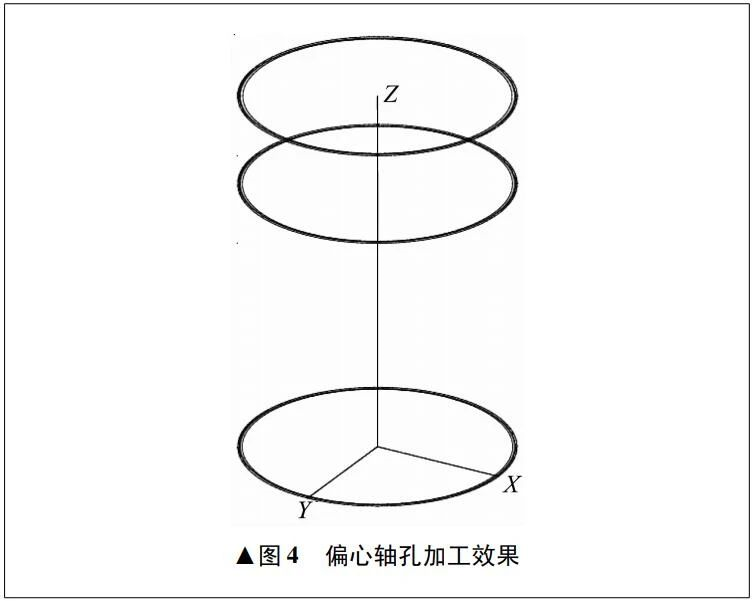
3.2 偏心轴系高度误差
行星架刚性盘组件实际加工中出现了偏心轴系高度超差情况,且多次测量数据不一致,多件加工质量不稳定。
行星架刚性盘组件的偏心轴系高度指刚性盘卡簧槽上端面和行星架止推面之间的距离,实际使用过程中,这两处位置分别限制偏心轴系的两端。卡簧槽为环形窄深槽结构,难以观察其端面实际加工质量,且测量难度大。止推面一侧为凸出台阶位,观察及测量均较为方便。常规的工艺方案为卡簧槽采用勾槽刀加工,止推面采用端面平铣刀加工。为了保证偏心轴系高度的精度和加工质量的一致性,工艺方案变更为采用具有端面切削能力的勾槽刀,同一把勾槽刀既加工止推面又加工卡簧槽,但实际测量时仍出现测量数据不一致、加工质量不稳定的情况。用线切割设备将工件切开,观察卡簧槽上下端面,发现上下端面均有较大的翻边毛刺, 且较难去除。出现翻边毛刺的原因是先加工卡簧槽,镗孔余量大且镗孔过程中切屑向卡簧槽内翻转。卡簧槽为窄深槽,工件清洗过程中无法去除毛刺,导致偏心轴系高度值不稳定。
如果采用先镗削偏心轴孔再加工槽的工艺,那么加工卡簧槽时加工量大,且切削力大,会造成偏心轴孔质量不合格。尝试进一步优化工艺,先粗镗偏心轴孔,再加工卡簧槽,最后精镗偏心轴孔,这一工艺方案在很大程度上减少了翻边毛刺,但仍有精镗留下的翻边微小毛刺,且难以清理。最终采用首先粗镗偏心轴孔,然后加工卡簧槽,再精镗偏心轴孔,最后空余量加工卡簧槽去除毛刺的工艺方案,既保证偏心轴孔的精度,又避免卡簧槽内产生毛刺,偏心轴系高度误差得到了有效控制。行星架刚性盘组件加工现场如图 5 所示。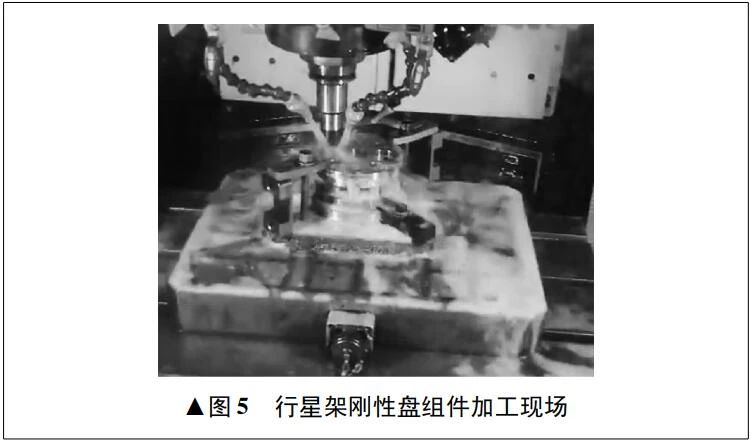
3.3 组件拆装后精度误差
行星架刚性盘组件加工完成时质量较好,但RV减速器装机过程中多次组装后,精度明显下降。
对行星架刚性盘组件的定位、连接情况进行具体分析, 组件由两个定位销孔进行准确定位, 再由四个螺栓锁紧,拆装过程中组件的重复精度由定位销孔定位精度决定。当圆柱销定位采用间隙配合时,由于存在销孔间隙,精度较低。如采用过盈配合,则拆装难度大,且重复性差,因此通常采用锥销定位。然而采用锥销定位后精度仍然常有波动,因此对锥销定位进行分析,如图 6 所示。销孔的实际锥度比为 1∶n1,n1 为锥孔锥度。锥销的锥度比为 1∶n2, n2 为锥销锥度。两者之间存在一定的差异。锥孔为锥铰刀成型加工,其锥度由锥铰刀决定。锥销为磨削加工,一般采用标准件。评估销孔的锥度采用计算式( d2-d1) /(Z2-Z1),d1为销孔下端直径,d2为销孔上端直径,Z1为销孔下端对应高度值,Z2为销孔上端对应高度值。当 n1大于n2时,销孔和锥销为上端线接触,下端存在间隙,间隙值为(1/n2-1/n1) ( Z2-Z1)。当n1小于n2时,销孔和锥销为下端线接触,上端存在间隙,间隙值为( 1 /n1-1/n2) ( Z2- Z1) 。由此可见,可以用计算式 | 1 /n2-1 /n1 |( Z2-Z1)/2 来评估锥销定位的重复精度。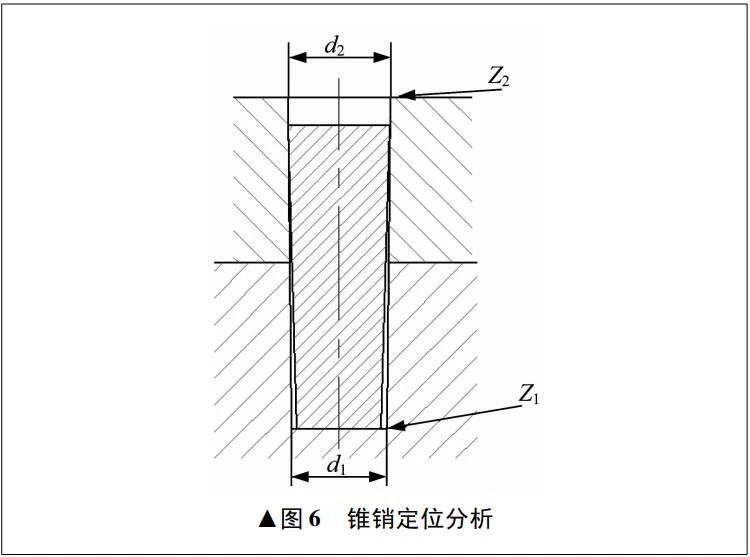
采取针对性控制措施,由于锥销采用外圆磨床加工,锥度相对容易控制,因此可以先加工锥孔再配磨锥销。采取上述控制措施后,行星架刚性盘组件的拆装定位重复性得到了有效改善,各项精度均满足要求。
4 结束语
RV减速机广泛应用于工业机器人、航空航天等领域,行业的发展和产品的更新迭代对RV 减速机及其零部件提出了更高效率、更高精度的要求,促使工程技术人员在设计加工方案时精益求精。对RV减速机行星架刚性盘组件精加工进行研究,有效保障了行星架刚性盘组件的加工精度和质量稳定性。